Folding reconfigurable materials : Toolkit to design metamaterials with programmable shape and function
During his PhD research at Harvard University, AMOLF group leader Bas Overvelde developed a smart method for designing and investigating new metamaterials. For such materials the microstructure determines the function, rather than the molecular composition. The ideal metamaterial changes shape autonomously to achieve the desired functionality. Overvelde and his American colleagues developed a toolkit to design such metamaterials that can assume different shapes in a manner reminiscent of origami. They published their research on 19 January 2017 in Nature.
In the case of many metamaterials, the unique microstructure is what makes them ideally suitable for one specific task, for example deflecting or conducting light or sound, or damping vibrations. “Our ideal was to design metamaterials that can assume different three-dimensional structures and therefore have adaptable functionality,” says Bas Overvelde, who obtained his doctorate in 2016 under the supervision of professor Katia Bertoldi at the Harvard John A. Paulson School of Engineering and Applied Sciences.
Origami-like
Overvelde and Bertoldi collaborated with designers to develop a strategy to systematically tackle the design of reconfigurable metamaterials. The basic shape in the design is a regular polyhedron, in which square or right-angled surfaces are always placed on the ribs so that a three-dimensional structure arises that is reminiscent of a folded origami shape. Overvelde: “The structure can fold at the edges between two surfaces. The relationship between the stiffness of the surfaces and the folding lines determines the behaviour of the eventual metamaterial and therefore how simply the material can change shape.”
Stiffness
The researchers developed a model in which they used simple mathematical shapes to design a multiplicity of different structures and identify their possible configurations. For some metamaterials obtained using their design strategy, the researchers built 3D structures with surfaces of cardboard and fold lines of double-sided tape. Although these model structures were merely intended to illustrate the concept, they nevertheless clearly showed the impressive ways in which these materials can change shape.
“The strength of our model is that it is completely scalable,” says Overvelde. “It does not matter whether the final material is metres high or on the scale of nanometres. As long as the ratio between the stiffness of the surfaces and the hinges remains constant, the shape – and therefore the functionality – changes in the same manner.”
Scalability also means that these metamaterials have many possible applications: from programmable photonic materials at the nanometre scale to metres-high architectonic constructions. Overvelde: “Specialists can use our toolkit to design metamaterials for their specific discipline.”
Sensors
Following his PhD research Overvelde started the Soft Robotic Matter group at AMOLF, where he is further investigating the shape changes in metamaterials. “By using active elements and sensors the forces that cause a metamaterial to change shape do not have to be applied externally but are realised internally,” he says. “By combining knowledge from robotics and metamaterials we can design materials that respond actively and non-linearly to the environment.”
Reference
Johannes Overvelde, James Weaver, Chuck Hoberman and Katia Bertoldi, Rational design of reconfigurable prismatic architected materials, Nature 541, 347-352, 19 January 2017. DOI:10.1038/nature20824
Video credits: Leah Burrows
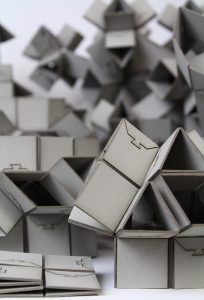
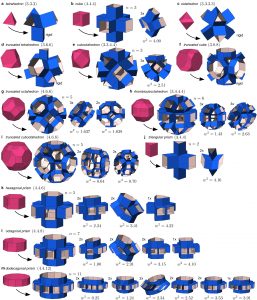